何がどのように入るか???
対象異物と伝達経路が分かれば、対策を講じます。
具体的には以下8アクションになりますが、その中で、
1.排除、2.最少化、3.制限 の能動的な戦術と
4.管理 の受動的戦術、
4つを効果的に組み合わせることが対策を効果的に抜けもれなく実行することになります。それぞれは後述しますが、何より難しく考えない、難しくしないことが肝心です。難しくない代わりに全員参加。特性要因図を上手に活用するのと同じです。
では、具体的な一連のアクションです。
1. 発生源の特定
工場内で異物が発生する原因を特定します。
2. 経路の特定
発生した異物がどのように製品へ到達するかを分析します。
3. 工程限定
異物混入のリスクが高い工程を特定して集中対策を行います。
アクション1~3は特性要因図による根本原因分析と現場の潜在的異物検出調査で完了します。ここからが対策。
4. 徹底清掃
作業環境の清浄度を向上させ、異物残存を防ぎます。
- 方法: 清掃手順の見直し、使用する清掃道具や頻度の適正化。
5. 発生源対策
異物の発生自体を抑制します。
- 例: 工場内ブラスチック製器具の金属化、設備の老朽部分交換、設備のカバー設置、原材料の受け入れ検査強化、作業服規定の徹底。
6. 伝達経路対策
異物が製品に到達する経路を遮断します。
- 例: 空調システムでの気流制御、エリアごとの動線設計、防塵シートの活用。
- 方法: 作業エリアごとに動線とゾーニングを見直し、異物が移動しにくい環境を作る。
7. 検出体制の強化
最終的に異物を検出し、製品への混入を防ぎます。以下の装置を活用します。
- 金属探知機: 製品内の金属異物を検出。特に包装前後で使用。金属成分の検知範囲を設定。
- X線検査機: 製品内部の金属や骨、ガラス片などの異物を検出。異物検出率を上げるため定期校正が必要。
- パーティクルカウンター: 空気中の微小な浮遊物質を検出し、作業環境の清浄度を数値化。清浄度をリアルタイムでモニタリング。
- カラーソーター: 異物や欠陥品を色の違いで検出。特に乾燥食品や穀物類に有効。
8. 教育と意識向上、モニタリングと改善
作業者への教育と定期的な管理体制の見直しを行い、持続的な改善を図ります。
- 教育: 作業者に異物混入のリスクや予防策をトレーニング。具体例を用いた実践的な指導を行う。
- モニタリング: 異物混入状況や対策効果を定期的に確認し、データに基づく改善を実施。定期監査や異物マッピングを活用。
根本原因分析を終えたら、アクション4~6で排除・最少化・制限し、アクション7で管理します。
気を緩めてはいけません。アクション8でPDCAを回すことで、完全解決を目指します。
対策の徹底が肝要です。
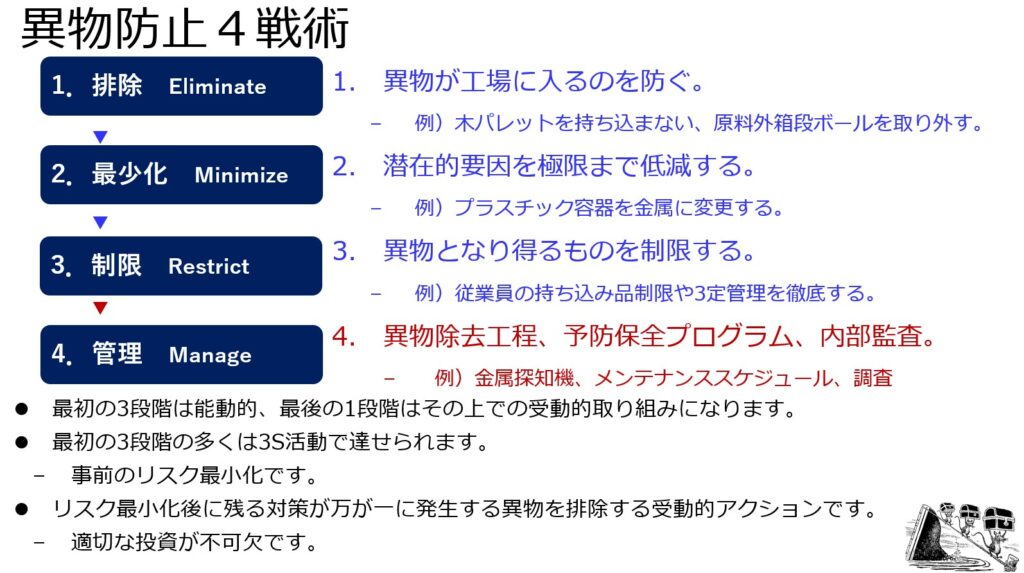
マス君お勧めの1冊:まずこれを読む!
異物不良「ゼロ」徹底対策ガイド-一般エリアからクリーンルームまで即効果が出る
異物の問題は食品だけで起きているわけではありません。そんなことも思い浮かばないくらいに近視眼的な世界で仕事をしていませんか?
先輩や上司の言うことを聞いているだけでは彼らの限界は超えられません。
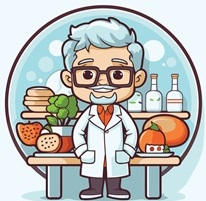