食品業界の技術者は貴重な専門知識を持っていますが、他の製造業の視点を取り入れることが成長と革新に繋がります。自動車、エレクトロニクス、化学など、他業界の手法は食品業界にも有益です。これらを取り入れることで、新しい視点を得て効率的な改善が可能になります。他業界の知見を積極的に学ぶことは、食品業界の進化と技術者としての成長に不可欠です。
既に述べた食品に混入する異物の対策は、究極、下記の8フレームワークに習熟することでかなりの効果を上げることが可能です。先生を同じ業界に求める必然はありません。分かったふりをしてきちんと勉強していない異エキスパートと呼ばれる者も少ないように感じます。改めて視野を広くとって基礎を学びませんか?
1.特性要因図
- 概要:異物混入の要因を体系的に図示し、根本原因を特定
- 有効性:複雑な要因の相互関係を視覚的に理解可能
- 事例:プラスチック片混入の分析で、作業手順・設備劣化・教育不足など多角的な原因特定により、効果的な対策を実施
2.現場ウォーク
- 概要:管理者による定期的な現場巡回と観察
- 有効性:現場の実態把握と即時の改善指示が可能
- 事例:ベルトコンベア周辺の目視点検で、ベルトの劣化による異物発生リスクを早期発見
3.3S活動
- 概要:整理・整頓・清掃による異物発生防止
- 有効性:日常的な活動を通じた予防的アプローチ
- 事例:工具管理の定位置化により、工具部品の紛失・混入を防止
4.層状プロセス監査 Layered Process Audit(LPA)
- 概要:複数階層による重層的な監査システム
- 有効性:異なる視点での確認により、見落としを防止
- 事例:各階層の監査で発見された課題を統合し、包括的な改善を実現
5.危険マッピング Hazard Mapping
- 概要:異物混入リスクの高いエリアを可視化
- 有効性:リスクの高い場所への重点的な対策が可能
- 事例:原料受入れ区域の高リスク判定により、検査体制を強化
6.改善 Kaizen
- 概要:現場からの小さな改善の積み重ね
- 有効性:現場の知恵を活かした実践的な改善
- 事例:作業者提案による検査ライトの角度調整で、異物の視認性が向上
7.TPM(Total Productive Maintenance)
- 概要:設備の予防保全による異物発生防止
- 有効性:設備起因の異物発生を未然に防止
- 事例:定期的な設備点検により、部品の緩みや劣化による異物発生を防止
8.PDCA
- 概要:計画→実行→確認→改善のサイクル
- 有効性:継続的な改善活動の基本サイクル
- 事例:異物検出件数の月次分析に基づく改善策の立案と実施
加えて、これらの8フレームワークの効果を最大化するポイントは下記の5点です。
- 統合的アプローチ :各フレームワークを単独ではなく、相互に連携させて運用する。
- 従業員参加 :全階層の従業員が参加する仕組みをつくり、現場の気づきを活かした実効性の高い改善を進める。
- リスク優先順位づけ :限られたリソースの効果的な配分により、重要度と緊急度に応じて対策に優先順位をつける。
- 継続的な見直し :定期的な効果検証と手法の改善により、現場状況の変化に柔軟に対応する。
- 文書化と標準化 :成功事例を文書化し水平展開することで効果的な取り組みを標準化する。
特に大事なのはフレームワークを利用しながらチームビルディングを目指すことです。異物の品質クレームがあったからと言って、少人数で小手先の対応をしてはいけません。多くの関係者の力を結集することが解決の原動力になります。
加えて若い世代は、管理職や熟練者の対応を見ていることを忘れてはいけません。彼らはロールモデルに飢えています。伝承を意識してこそ工場の企業文化が維持・向上されます。
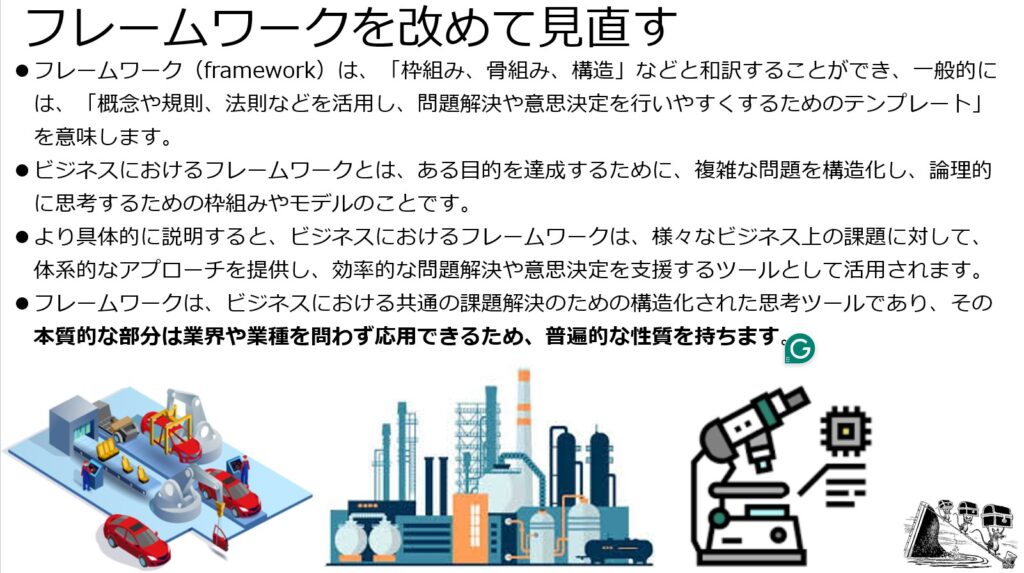
マス君お勧めの1冊:まずこれを読む!
ビジュアル ビジネス・フレームワーク[第2版] (日経文庫)
ビジネス・フレームワークを多数掲載。問題解決に当たっては、まず先人の教えを乞う。オリジナリティーの追求は多くの場合、時間の無駄。
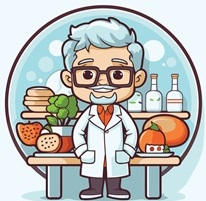