日本のメーカーの技術者はよく日本の品質は世界一だといいます。
そこには、下記の背景があります。
■ 高度経済成長期の成功体験
1950~70年代、日本は製造業で世界市場を席巻し、品質管理手法(TPSやカイゼン)が高く評価されました。この成功体験が「日本の品質は世界一」という自信の土台になっています。
■ 「品質第一」文化の定着
日本企業では、納期やコストよりも品質を優先する考え方が深く根付いています。現場から経営層まで「品質を守る」ことが当然とされ、技術者の誇りになっています。
■ 細部への徹底したこだわり
日本のモノづくりは、ミクロン単位の精度や外観のわずかな瑕疵も見逃さない「細部へのこだわり」が特徴です。これが他国との差別化につながっています。
■ 国際的な評価と認知
日本企業はデミング賞など国際的な品質賞を受賞し、「Made in Japan」が信頼の象徴となりました。こうした実績が、技術者たちの自負を支えています。
■ 技術者としてのプライド
日本の技術者は「品質では絶対に負けたくない」という強いプライドを持っています。自国の技術と品質を守り抜きたいという意識が、「世界一」という信念を支えています。
では、なぜ日本の品質管理や品質保証のやり方が世界標準にならないのでしょうか?
- やり方が「人に依存」しすぎている
「ベテランがなんとかしてくれる」という現場力への依存が強いです。これにより、標準化や仕組み化が後回しになりがちで、グローバル展開しにくい原因になっています。 - 文脈・暗黙知を前提にしている
日本では「言わなくてもわかる」「空気を読む」前提で品質管理が動いていますが、国際標準は「文書化・明示化」が前提です。これが異文化の人にとって非常にハードルになります。 - 過剰品質になりやすい
要求以上の品質を提供しようとしてコストをかけすぎたり、納期を守れなかったりするリスクがあり、「必要な品質+最適なコスト」を重視する国際競争では不利になります。 - 外部監査や第三者認証を重視しない
日本は「自社の信用」「取引先との信頼関係」で成り立つ文化がありました。対して世界では第三者認証(例:ISO認証など)が信用の担保なので、日本式は「なぜ公的に証明しないのか?」と不思議に思われがちです。 - 伝統を変えにくい
「これまでうまくいってきたやり方をなぜ変える必要があるのか」という心理が強く、環境変化に合わせたプロセス改革が遅れがちです。グローバル標準化の波に乗り遅れる一因になっています。
では、どうすれば国際的に通用する品質保証ができるでしょう?
こんな風に考えられませんか?
- 「人依存」から「仕組み依存」へ
誰がやっても同じ結果が出る標準作業をつくる
属人的なノウハウを可視化・共有する
教育訓練で全員のレベルを底上げする - 暗黙知ではなく「形式知化」を徹底
手順・判断基準はすべて明文化する
口頭伝達に頼らず、文書や図で残す
記録・エビデンスを常に意識する - 過剰品質を防ぎ「目的基準」で考える
顧客要求と契約条件を正しく理解する
「必要十分な品質」ラインを設定する
コスト・納期とのバランスで最適解を探る - 第三者認証・外部監査を積極的に活用
国際認証(ISO等)の取得を積極推進する
外部監査の結果を謙虚に受け止め改善する
社内チェックと外部基準の両輪で運用する - 伝統を守りつつ「変える力」を育てる
守るべき価値(安全・信頼)を明確にする
時代に合わない慣習は見直しを恐れない
デジタルツールや新技術を積極導入する - 英語力不足・国際発信力の弱さ
技術や手法を英語で体系化・標準化する
国際的な活動、会議に積極参加する
日本独自の強みを世界に伝える発信力を磨く
「知られていないことは存在していないのと同義」という考え方は、現代のマーケティングにおいても出発点として有効とされます。なぜなら、どれほど優れた商品やサービスであっても、消費者にその存在が認知されていなければ、興味や関心を持たれることもなく、購買行動につながることもありません。認知は消費者の購買プロセスの最初のステップであり、ここを通過しなければ次の「興味」「検討」「購入」といった段階へ進むことはできません。
日本の品質が本当に世界一でも、知られてない、広まらないのはとても残念なことです。国際発信力の強化を含めて将来のありようを考えるべきではないでしょうか?
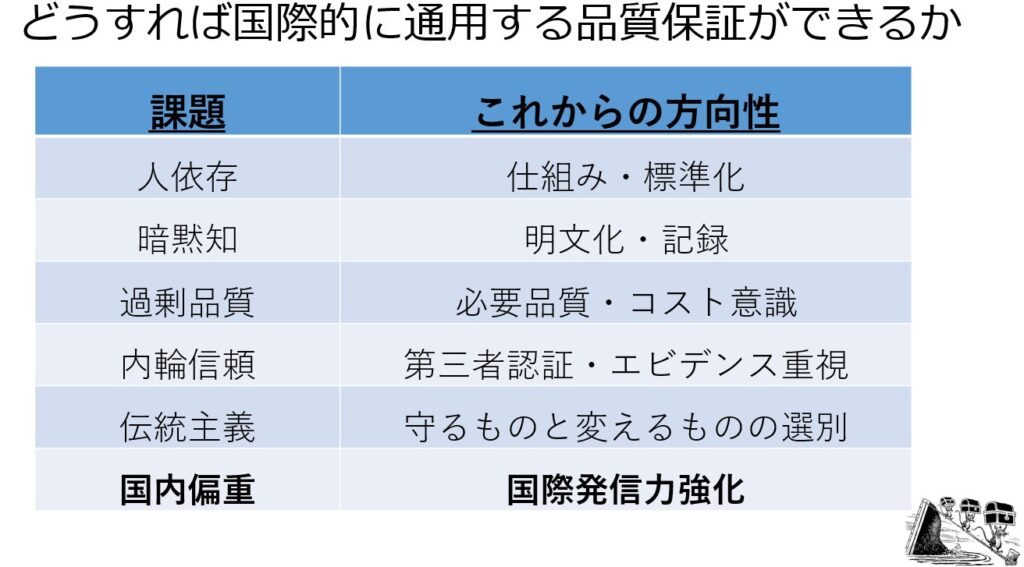
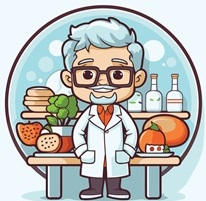