特性要因図を使用した根本原因調査の進め方は下記のとおりです。
1.問題の明確化
- 品質保証部門が原則ファシリテーターに就きます。分析の対象となる品質不良を明確に定義し特性とします。
- 担当部門を設定し分析チームメンバーを選任してもらいます。生産部門(製造・品管)、購買部門、工務保全部門、製品開発部門に加え、必要に応じて教育を担うなどが人事・総務部門や営業部門など非製造関連部門も含めます。
- 「製品に異物が混入していたことをと特性を設定する。これに適切な付帯情報を提供する。例えば、
- その異物が金属片なのか、プラスチック片、或いは他の何なのかの材質、寸法、形状などの情報。
- 過去の同様事例の有無。
- バイアスを与えない範囲で想像されるその発生場所(製造ライン、包装ラインなど)を示唆します。
2.問題の明確化
- 特性要因図の準備
- 問題を引き起こした要因を視覚的に整理するために、空白を十分に確保したテンプレートを作成します。
- 要因の大骨部分の設定。推奨は下記4M+Eの5つ。
- 人(Man) : 操作ミス、教育不足、作業者の疲れ
- 機械(Machine) : 設備の老朽化、故障、調整不良
- 方法(Method) : 作業手順の不備、標準化の不足
- 材料(Material) : 原料の品質不良、輸送中の破損
- 環境(Environment) : 温暖化による温度や湿度の高さ、騒音、労働負荷。
- 経営(Manegement):上記5要因の発生現場に留まらないものに関し必要な場合に限り経営を加えるのは可です。
肝心なのは基本的に同じテンプレートを使用し、習熟度を上げることです。
3.要因収集
- 要因に関する情報収集(個別ブレインストーミング)
- 担当部門にテンプレートを配布し、期限を設定したうえで、入力を依頼します。
- テンプレートに入力する際に使用する色を各部門に割り当てます。
- この時点では分析チーム内でディスカッションをしてはいけません。分析チームメンバーは所属部門の専門的見解を尊重し入力します。
- 各部門内で短期集中のディスカッションが肝要です。特に重要なのは熟練者の経験談です。埋もれた情報の発掘機会です。
- 各メンバーは所属部門に持ち帰り、特性要因図に入力すべき要因をすべて入力します。
- 可視化・形式知化が目的なので、明らかに関連性がないものは除くとしても、否定や排除をしてはいけません。原則としてすべて記録します。ブレインストーミングと同じです。
4.要因の集積知化
- 要因に関する情報収集(個別ブレインストーミング)
- 各担当部門より提出された入力済み特性要因図を品質保証部門が、俯瞰できるように一つのテンプレートに集めます。
- 入力量や明瞭性の課題を明確にし、再度、要因を集積したテンプレートを各メンバーに配布し同様作業をもう1度依頼し、入力漏れがない状態にします。
- 2回の入力作業を経て記入されたテンプレートが集まった後、品質保証部門が重複や新たな視点を補完します。
5.仮説の検証
- 品質保証部門は集積知化した入力済テンプレートを分析チームで共有します。
- 分析チーム会議を招集し、仮説を検証して根本原因を特定します。
- 特性要因図に挙げられた要因を元に、実際に関連データを検証します。
- 入力の重複と重要度を考慮し、これまで見過ごされていた発見に特に着目します。
- 原因や背景に対する仮説を立てます。要因同士を結びつけることで浮かび上がってきます。
- 各仮説がどれだけ実際の問題と一致しているかを確認し、有力な仮説を絞り込みます。
- 原因を特定します。
6.対策の検討と実施
- 根本原因を取り除くための具体的な改善策を決定します。
- 根本原因ごとに改善策の実施計画を立て、PDCAプランを立てます。
- PDCAプランを難易度と貢献度から優先順位をマッピングします。
- 改善策が決まった後、実施計画を立てて各部門で対応します。
7.結果の評価とフォローアップ
- 品質保証部門は実施後の製品やプロセスをモニタリングし、品質不良が再発しないかをチェックします。
- 関連部門に状況をフィードバックし、必要に応じて改善策をさらに強化します。完了する改善策があれば、重要度マッピングを再検討します。
2回の入力作業が発生する4.要因の集積知化 を考慮すれば根本原因分析に要する時間は最大2週間。入力作業を2回にしなくでもよいと判断されればより短い時間で根本原因分析は終えられる筈です。肝心なのは基本に手を抜かないことです。
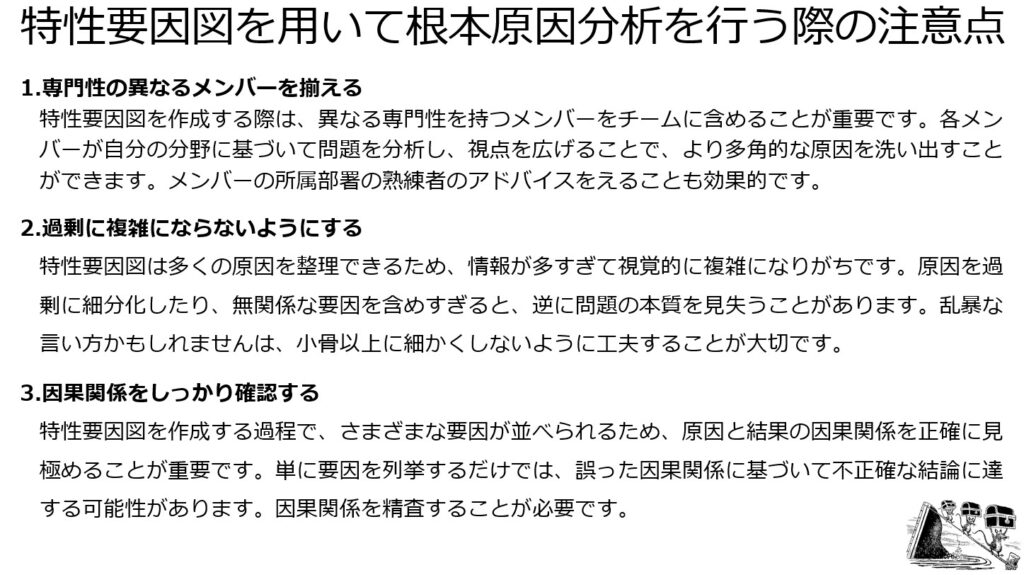

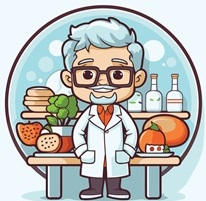