実践で得た知見を基に問題解決や意思決定を効率化することが経験則に学ぶということです。
経験則に学ぶことは事故対策の要であり、過去の教訓を活かすことで再発防止や初動対応の迅速化が可能となります。現場で培われた対応策は実効性が高く、影響を最小限に抑えるだけでなく、組織全体の危機管理能力向上や改善文化の醸成にも寄与します。
ただし、食品工場の異物混入対策では、経験則に固執せず、最新の知見を組み合わせて活用することが重要です。たとえば、過去の経験則から「異物は作業場の定期的な清掃と点検で減らせる」と考え、全エリアを同じ頻度で清掃する取り組みが一般的でした。しかし、積極的な取り組みとしては「作業環境の微生物や異物の分布マッピング」を活用することで、異物が発生しやすい高リスクエリアを科学的に特定することが可能になります。
分布マッピングでは、工場内の床や機器周辺、空調口などを定期的にサンプリングし、異物や微生物の濃度や種類を分析します。このデータをもとに、異物発生リスクが特に高い箇所を明らかにし、清掃や点検の優先順位を最適化することができます。たとえば、頻繁に清掃していたエリアが実際にはリスクが低く、逆に見落としていた場所でリスクが高いことが分かる場合もあります。
このように、過去の経験則を土台としながらも、分布マッピングという最新技術を組み合わせることで、清掃や管理の精度が向上し、無駄を省きながら効果的な異物混入対策を実現することができます。経験則だけでは捉えきれない問題を解決するために、最新の知見を柔軟に取り入れる姿勢が求められます。
1. 異物の発生源と潜在的な異物を特定する(特性要因図の使用)
まず、異物混入のリスクを把握するために特性要因図(フィッシュボーン図)を活用します。異物が発生する原因を以下のカテゴリーで整理します:
- 人(Man) :服装、手袋、作業習慣、教育不足など
- 機械(Machine) :機器の不具合や欠陥、設置場所など
- 材料(Material) :原料自体の不純物や供給元の品質問題など
- 方法(Method) :規定や手順、監視体制の不備など
- 環境(Environment) :湿度、温度、清掃状態など
特性要因図を使用して、異物が発生しやすい具体的な場所やプロセスを洗い出し、その後の対策に必要なデータを収集します。
2. 異物の種類や発生リスクのデータ収集
異物が発生するリスクの高いエリアを特定するため、工場内の異物や微生物の発生データを収集します。これには、以下のような情報を含みます:
- 異物の種類 :金属片、プラスチック、木片、毛髪など
- 発生場所 :作業台、機器周り、床、空調口など
- 発生頻度 :異物が発見された頻度
- 環境条件 :湿度、温度、換気状態など
これらのデータを集めるために、サンプリングやモニタリングを調査時のみならず以降も定期的に行います。発生場所やリスクの頻度を科学的に特定することで、必要な改善策を立てやすくなります。
3. 異物のサンプリングと現場作業者の技量向上
現場作業者が簡単に使用できる異物検出ツールを導入し、作業者が経験を通じて学べる環境を作ることが重要です。以下のようなツールを例に挙げます:
①目視検査とチェックリスト:定期的な目視検査に加え、チェックリストを活用して異物発見の兆候を見逃さないようにします。必要に応じて普段目視確認指定に場所に着眼します。作業者が検査結果を記録することで、その重要性を再認識し、自己学習が進みます。
②白い手袋(ホワイトグローブ):機器・設備の清掃が十分に行われたかどうか、また作業環境が汚れや潜在的な異物で汚染されていないかを確認するための簡易的な検査方法です。作業者は白い手袋をはめて、対象物の表面を軽く撫でます。白い手袋は汚れや異物を明確に表示するため、汚れの検出が容易になります
③粘着テープ:作業エリアや製品表面をチェックするために粘着テープを使い、目に見えない微細な異物(ホコリや毛髪など)をキャッチする方法です。作業者はテープを使って定期的に異物をチェックし、その結果を記録することで学びます。
④UVライト:UVライトを使用して、目視で確認しづらい異物を明らかにする方法です。特に、微生物や油分の異物が検出されることがあり、作業者が実際に光を照射して異物を特定し、その処理方法を学びます。
⑤異物の記録と分析:発見された異物は、適切に分類・記録し、発生源の特定や今後の予防策に役立てます。
4.伝達経路特定
潜在的異物を現場で採取し、それを同定することは、異物がどのようにして半製品に入るかを特定する上で非常に重要です。採取された異物を分析することで、その発生源や伝達経路を明らかにする手がかりを得ることができます。たとえば、金属片であれば設備の摩耗や工具の欠損、プラスチック片であれば包装材の破損や作業中の取り扱いミスなど、異物の種類と特徴から発生源を推測できます。また、その位置や発見されたタイミングから、異物がどの経路を通って混入したのかを特定することが可能です。
5. 異物の分布マッピングを作成
収集したデータをもとに、作業環境内での異物や微生物の分布マッピングを作成します。工場内のレイアウト図やフロアプランに、異物が発生しやすいエリアを色分けやマークで示します。これにより、以下のようなアクションが可能になります:
①高リスクエリア:異物発生が多い場所や微生物の数が多い場所には強調して色分けし、優先的に清掃や点検を行います。
②低リスクエリア:発生頻度が少ないエリアを特定し、最小限の管理で済ませることができます。
この分布マッピングにより、リソースを効率的に配分し、管理を最適化することが可能になります。
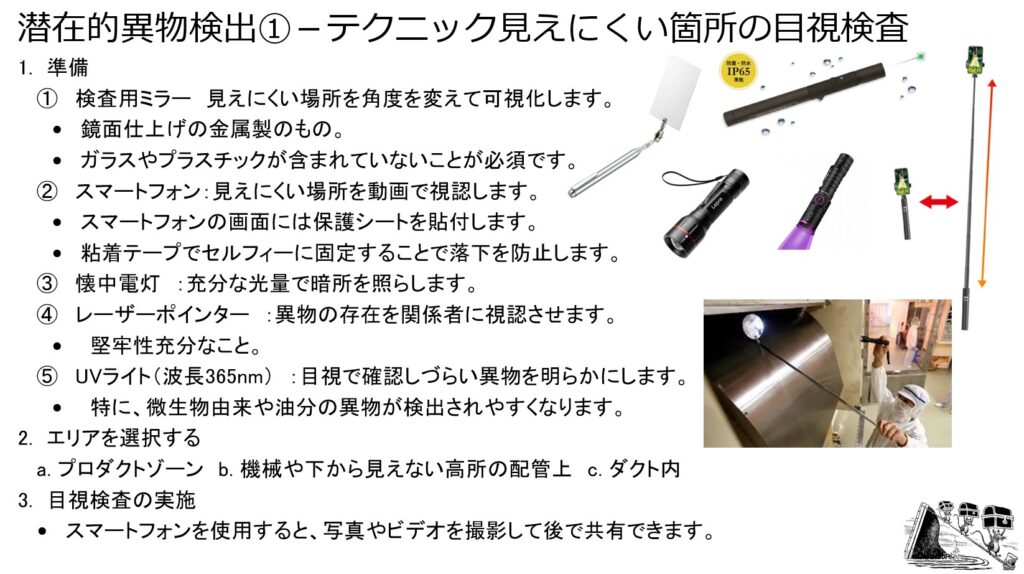
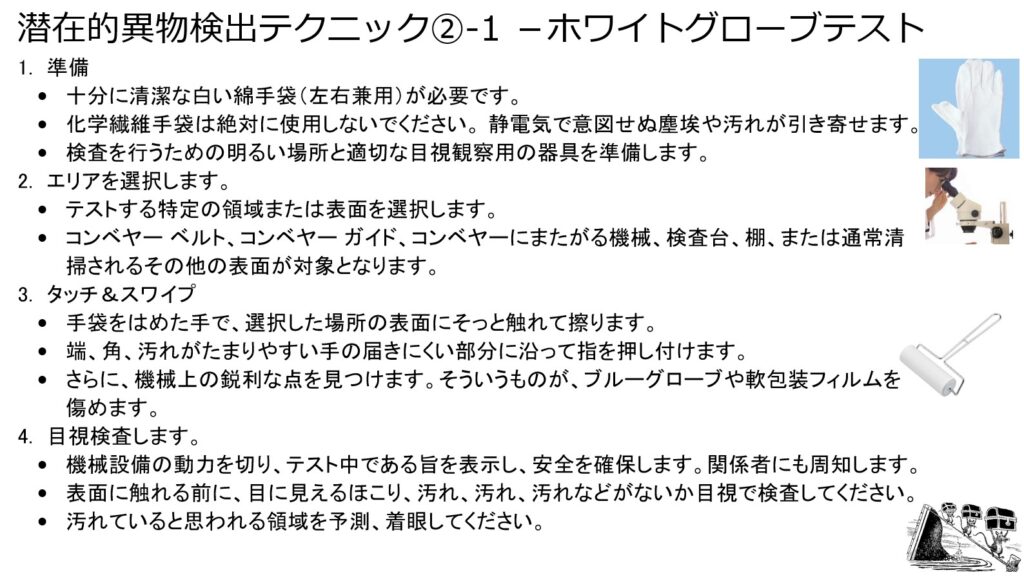
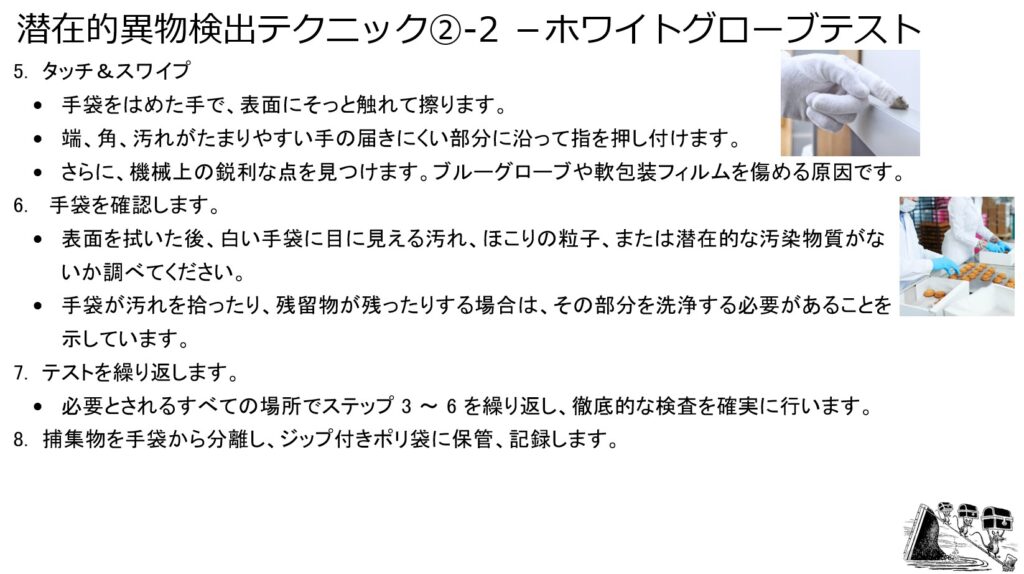
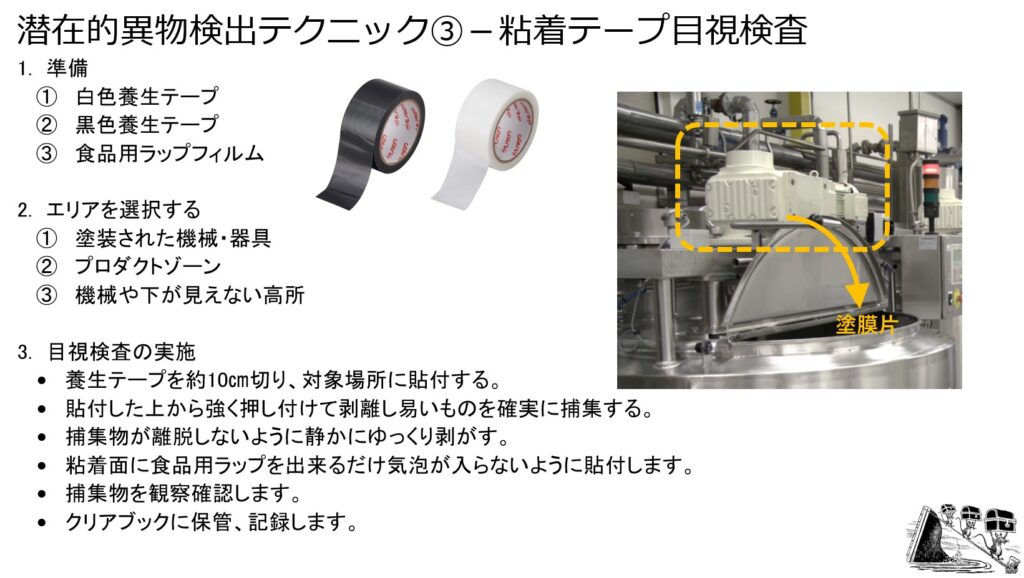
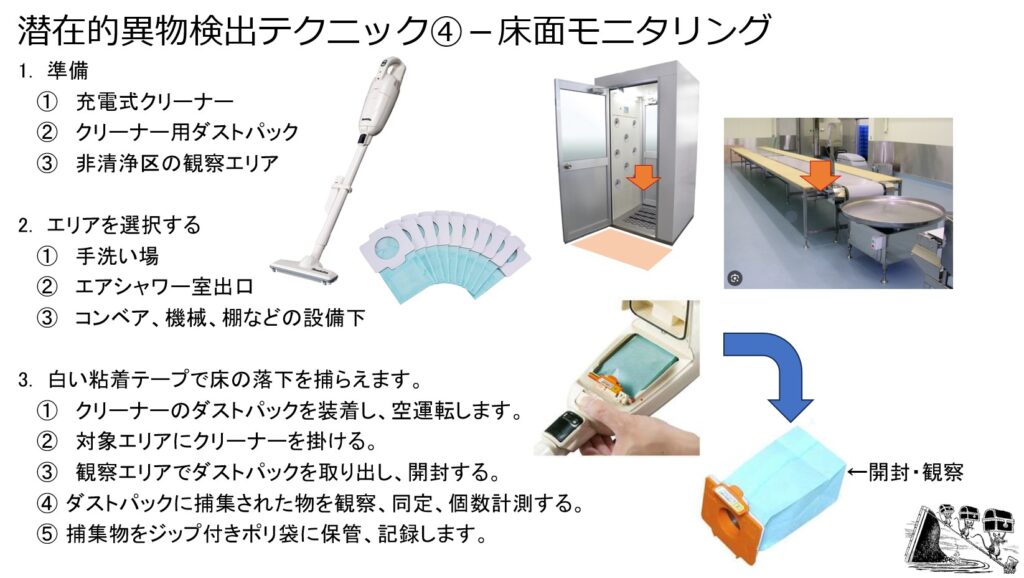
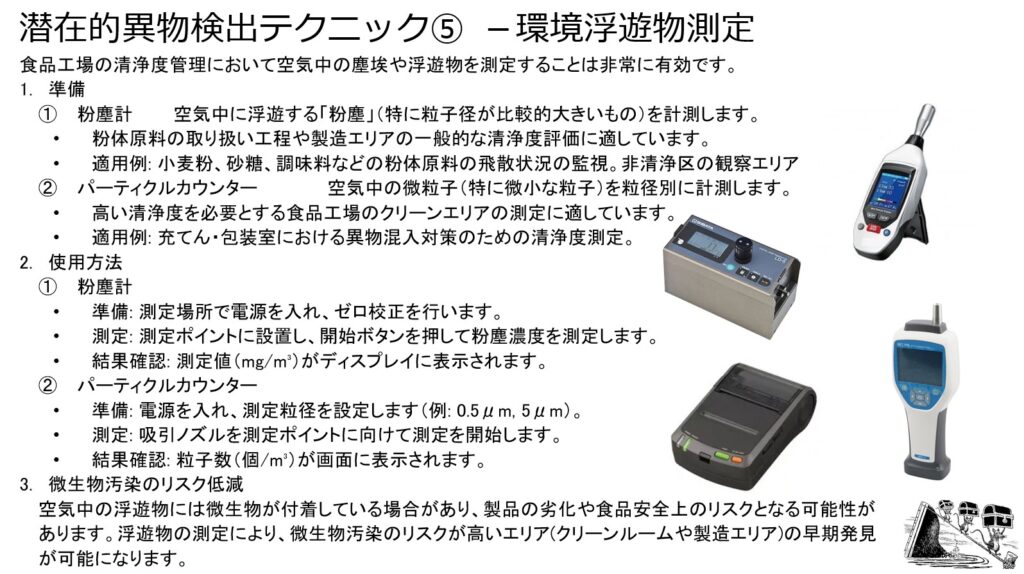
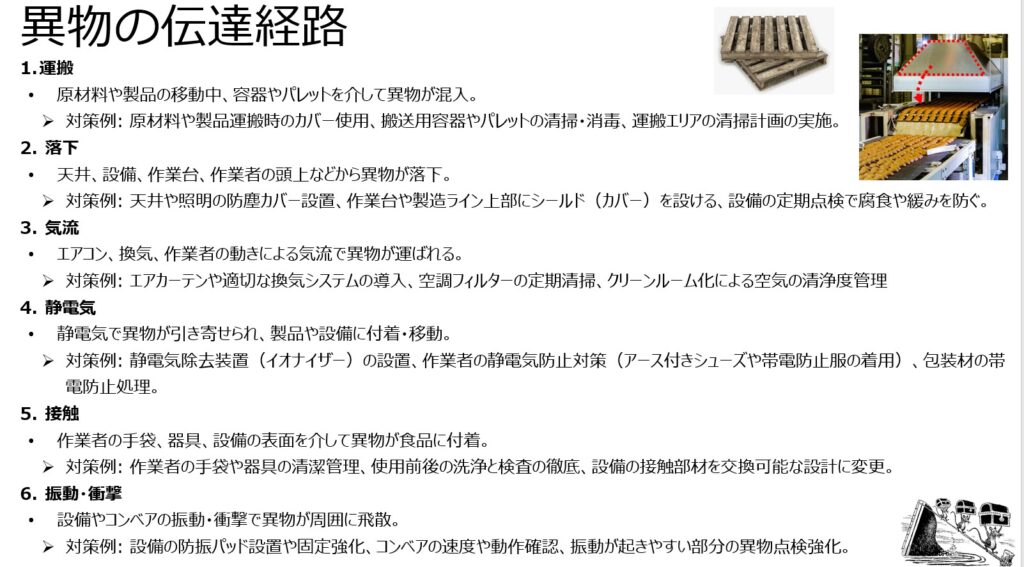
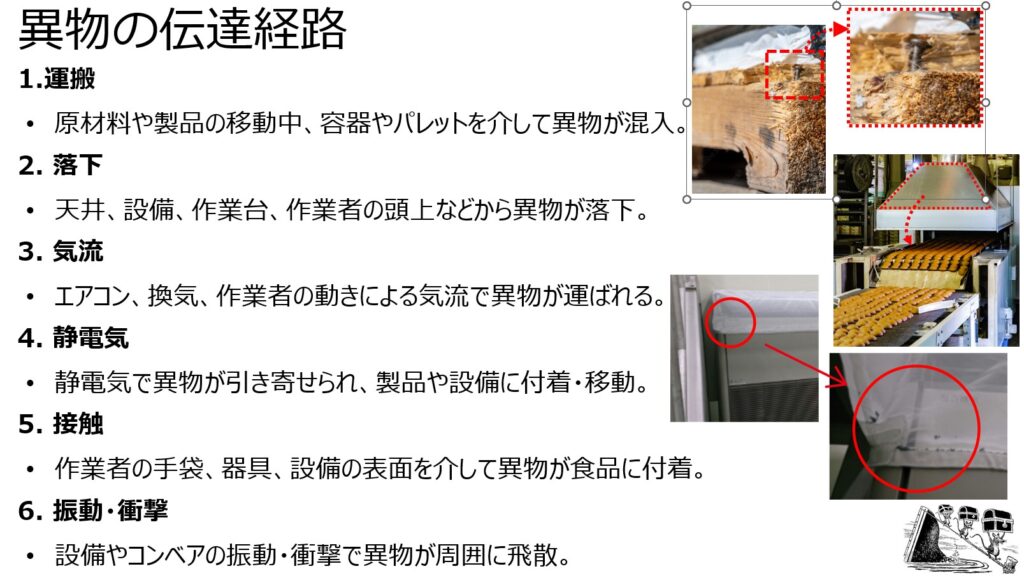
マス君お勧めの1冊:まずこれを読む!
彼を知り己を知れば百戦殆からず。敵を知らずに戦術も戦略ありません。無駄撃ち、無駄死にあるのみです。
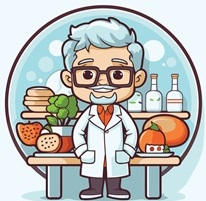